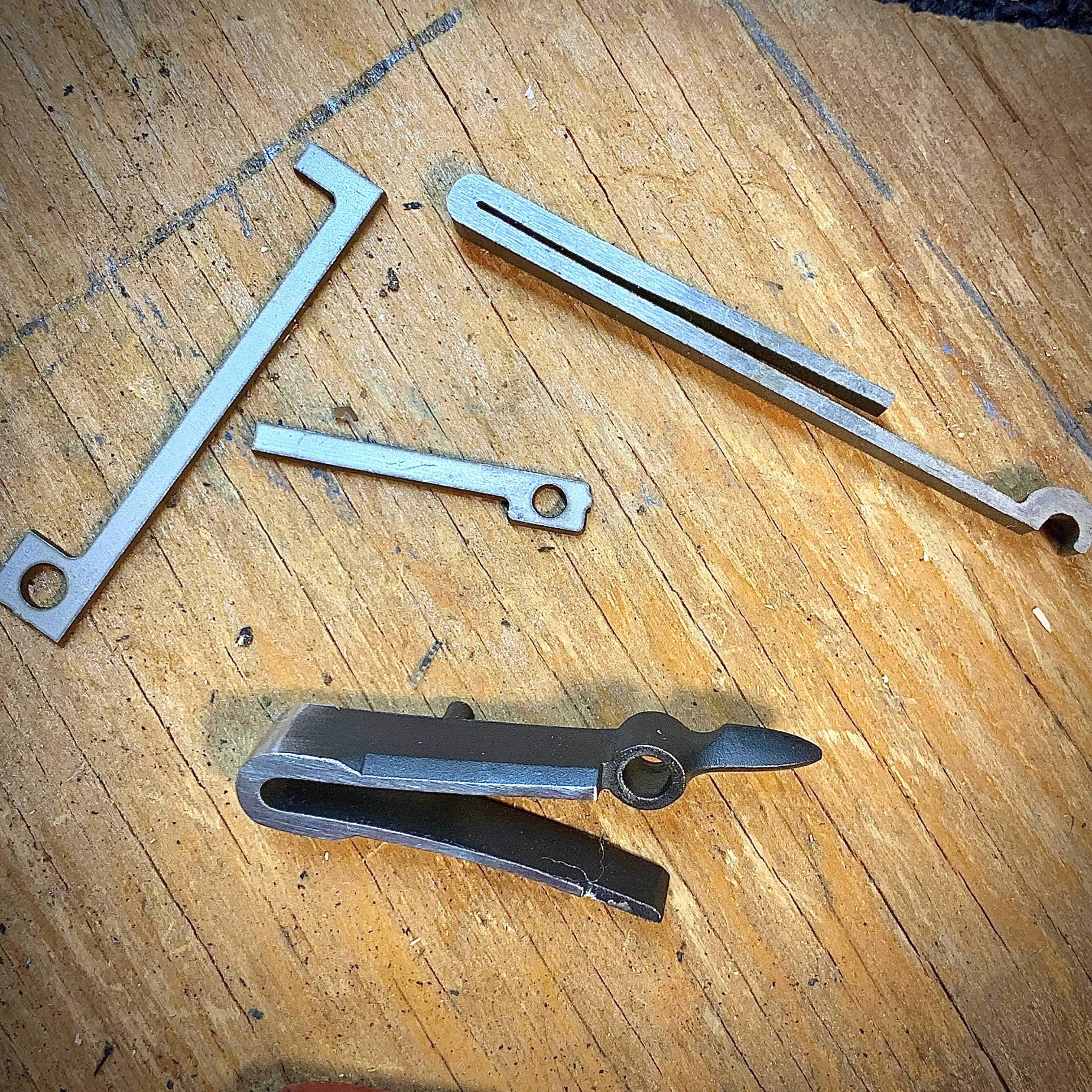
A properly made gun spring is only as good as the material it was made out of. Choosing the right type of steel is the first step in any spring-making endeavor. Springs can be made using many types of steel, but some work better for gun springs than others. 1075, 1095, 6150 are all commonly used today for making gun springs, but which will work best for your application?
Affiliate Disclosure: This article may contain affiliate links. When you use these links, I earn a small commission from each sale generated at no cost to you. This commission helps me continue to put out free content. I work a full-time job that I am very happy with; therefore, I don’t need this commission and am not obligated to speak highly of any product. Everything written is my own opinion: the good, the bad, and the ugly.
Understanding Steel Basics
Steels are made and sold using a four-digit number system to denote their physical properties. These four numbers tell you everything you need to know about the steel you are working with. For this article, we are only going to focus on the properties of spring steels used in gun springs.
The first number in the four-digit numbering system denotes the type of alloy primarily being used. The list on the right is a great reference for this.
The second number denotes any top-grade elements.
The last two digits indicate the amount of carbon that it contains. This number is often referred to as how many “points of carbon” it has. For example, 1075 steel will have 0.75% carbon content or 75 points of carbon.
For an extensive list of steel types and components click here.
- 1XXX – Plain Carbon Steel
- 2XXX – Nickel Steel
- 3XXX – Nickel-Chrome Steel
- 4XXX – Molybdenum Steel
- 5XXX – Chromium Steel
- 6XXX – Chrome-Vandium Steel
- 7XXX – Tungsten Steels
- 8XXX – Nickel-chromium-molybdenum steels
- 9XXX – Silicon-Manganese Steel
Ideal Properties of Gun Spring Steel
When it comes to the ideal properties of steel for a gun spring, it really doesn’t differ that much from steel used in automotive spring steel. The strength, ductility, and fatigue resistance are very much the same. The property that is needed for a gun spring that isn’t needed in the automotive world is machinability.
Most leaf or flat style springs in the automotive industry are cast and are pretty simple when it comes to their shapes. This is not the case in the gun industry. The shapes and bends sometimes needed, require that the material is easy to work with and machine. Keep in mind that somewhat high carbon content is needed to make a good spring, so it will never be as machinable as some of the more mild steels.
As far as the carbon content is concerned, in Simplified V-Springs by Kit Ravenshear, he states “Primarily the right steel is plain, medium, carbon steel with a carbon content somewhere around 0.7%…. but can be as low as 0.5% and as high as 0.9%.”
Use coupon code KTG10 to get 10% off your order of $150 or more at Brownells.
Gun Spring Steel Options
The options listed below are not the only options out there, however, they are some of the most commonly used steels for spring-making in the gun industry. All of the steels listed below have excellent spring properties and will do their job.
1075
Plain carbon steel with 75 points of carbon, is an excellent option for making gun springs. It is easier to work with and heat treats easier than some of the other options. If forging this steel to shape, you are going to want to anneal it after getting your final shape and before hardening it.
Working with 1075:
Annealing 1075 is achieved by heating the steel up to 1700 degrees Fahrenheit and allowing it to cool slowly in the furnace or burying it in sand or lime(Calcium Carbonate).
To harden 1075 steel you heat it up to 1650 degrees, using a carburizing flame and quench in oil.
To temper, heat 1075 up to approximately 700 degrees and allow it to air cool.
It is found in sheets and strips of various sizes and thicknesses, which is ideal for laying out some of the odd-shaped springs. Be sure to buy it in the annealed state to eliminate that step in the process.
1095
Plain carbon steel with 95 points of carbon, 1095 is another great option for making springs. Due to the higher carbon content, it isn’t as machinable as 1075 but that doesn’t mean that it isn’t doable. 1095 makes excellent spring steel, but another downside is that you need to be precise with your temperature during the hardening process. This is best done with a furnace. Doing it by judging the color by eye is possible but not as consistent as 1075. As stated with 1075, it is best purchased in the annealed state to eliminate the extra step.
Working with 1095
Annealing 1095 is done by heating it up to 1650 degrees and allowing it to slow cooly in the furnace.
To harden, heat the piece up to 1650 Degrees and quench in oil.
Tempering is done at 700 degrees.
1095 is also found in both strips and sheets. 1095 can be found in strip form at Brownells here.
6150
6150 is a carbon chromium alloy steel that is most commonly used to cast springs in the gun industry. Many of the casting kits that you will find on the internet will come with un-heat-treated springs made of 6150.
Working with 6150
Annealing is done by heating to 1550 degrees and allowing it to slowly cool.
To harden, heat to 1600 degrees and oil quench.
Tempering is done between 650 and 700 degrees.
It is unlikely that you will be buying strips of 6150 to make into springs. What is more likely is that you will be buying a cast replacement spring from somewhere like Track of the Wolf and having to do the final polishing, shaping, and heat treating.
How to Choose Steel for a Gun Spring
As mentioned earlier, all of the above steels are excellent for gun spring making. So how do you choose which material to use? I personally think it comes down to what is available or what you have on hand. If I had to choose one to keep stock of it would be 1075. In my current shop setup, it is easier to work with. Whenever I am able to get a heat-treating furnace that might change.
While casting has gotten a bad rap over the years, there is no reason why you should avoid cast springs. Most are of excellent quality and are by far the most affordable option for things like muzzleloader mainsprings.

Written by: Kurt Martonik
Kurt is a Gunsmith, Reloader, Hunter, and Outdoorsman. He grew up in Elk County, Pennsylvania, where he became obsessed with the world of firearms. Following high school, Kurt enlisted in the United States Air Force as a Boom Operator, where he eventually rose to the position of Instructor. After his military service, he attended the Colorado School of Trades(CST) in Lakewood, CO for gunsmithing. Following graduation, he accepted a job at C. Sharps Arms in Montana, where he worked as a full time stockmaker and gunsmith.